Laminated board glue is an adhesive often used by wood processing plants and furniture manufacturers. Its main purpose is to glue multiple small pieces of wood into a whole board. Through our long-term experience serving customers, the cracking problem after using laminated board glue is also a common problem for manufacturers. Below, we will share with you the main reasons for cracking when using laminated board glue:
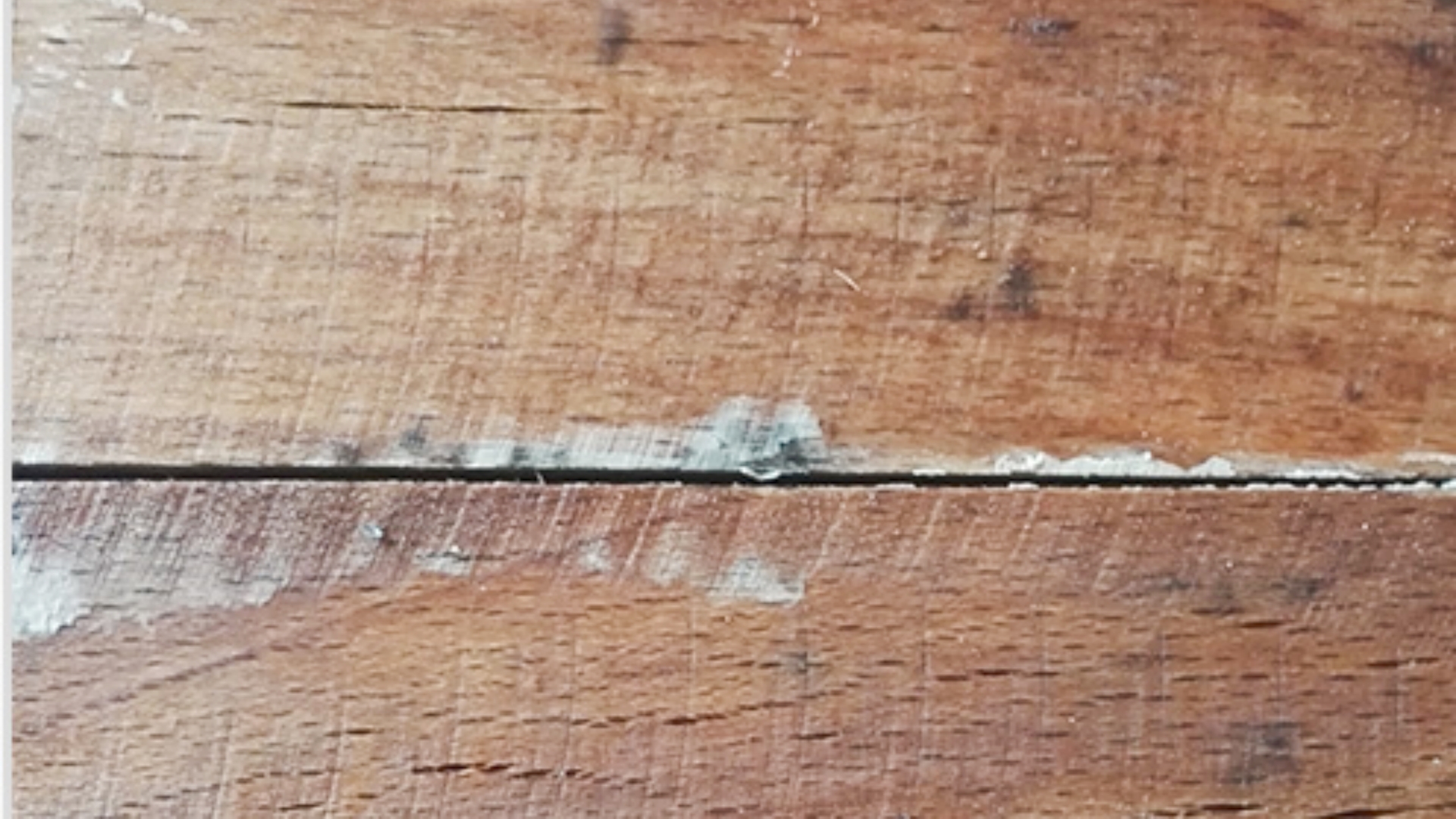
1. The moisture content of the wood is too high or too low

2. The hardener ratio is too low or too high
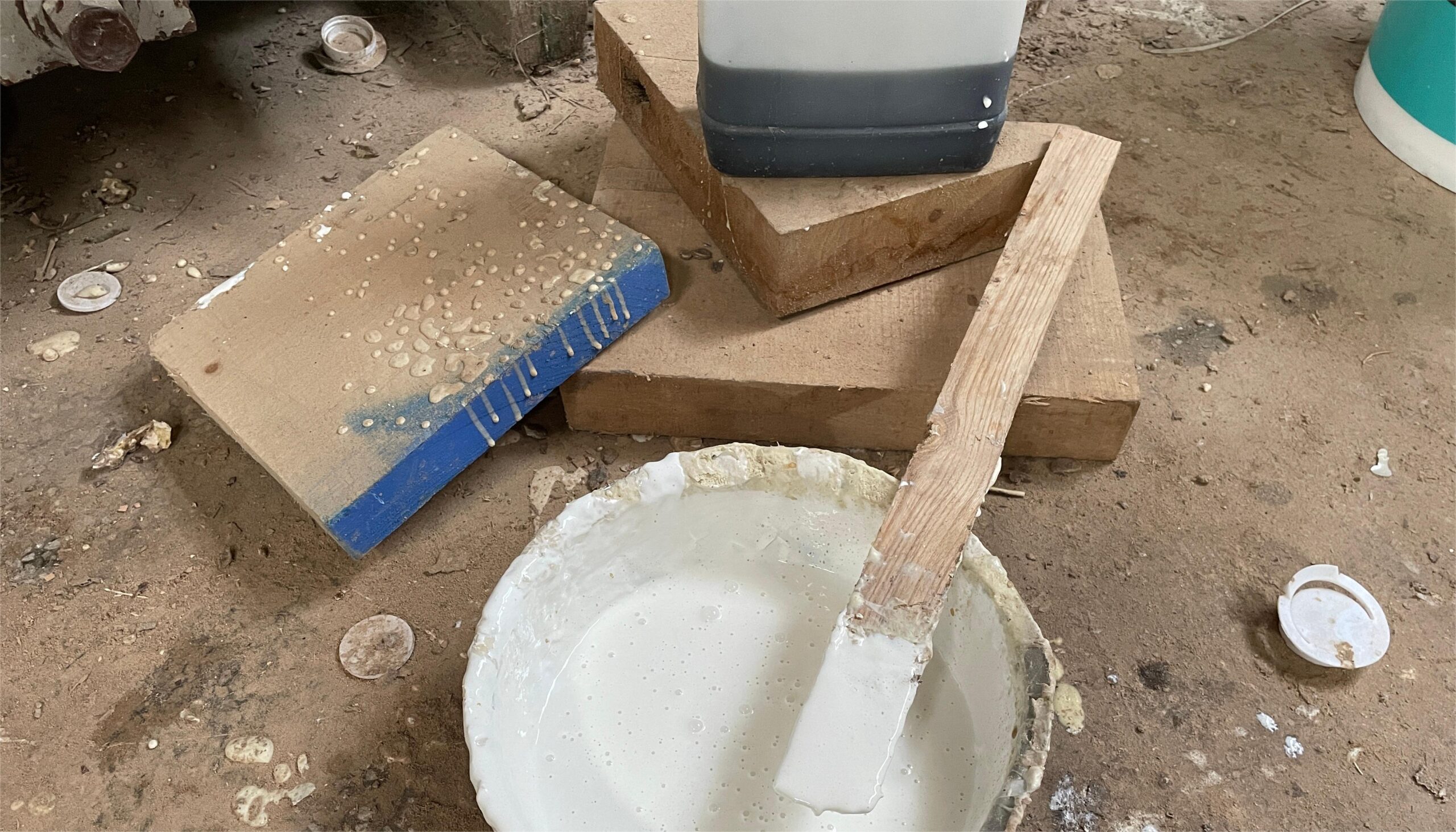
3. The pressurization time is too short and the pressure is too low
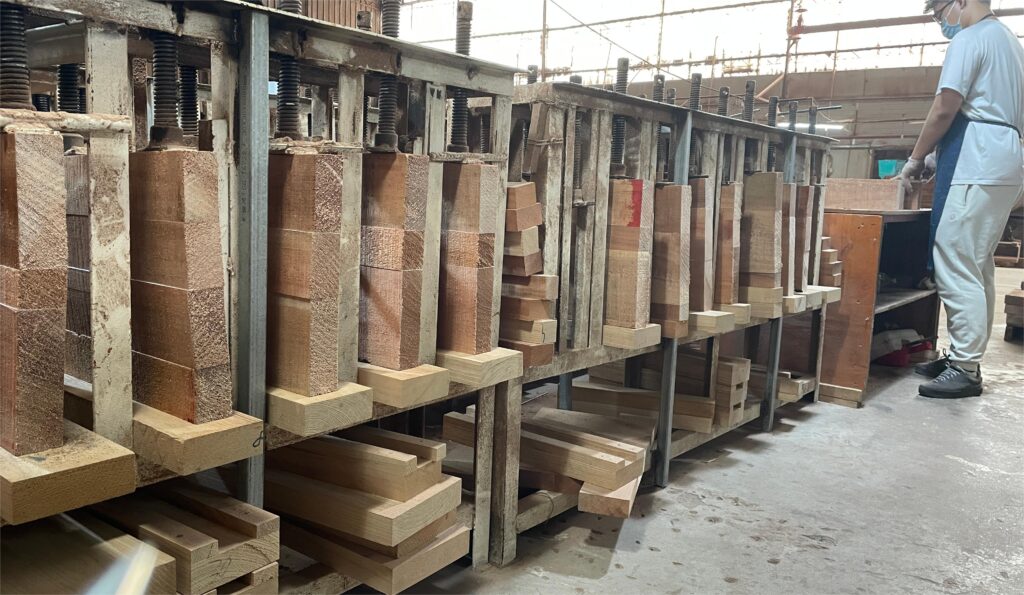
4. The processing precision of wood is not enough
5. The amount of glue applied is too low (after lamination, no glue overflow is seen at the joints of the boards)
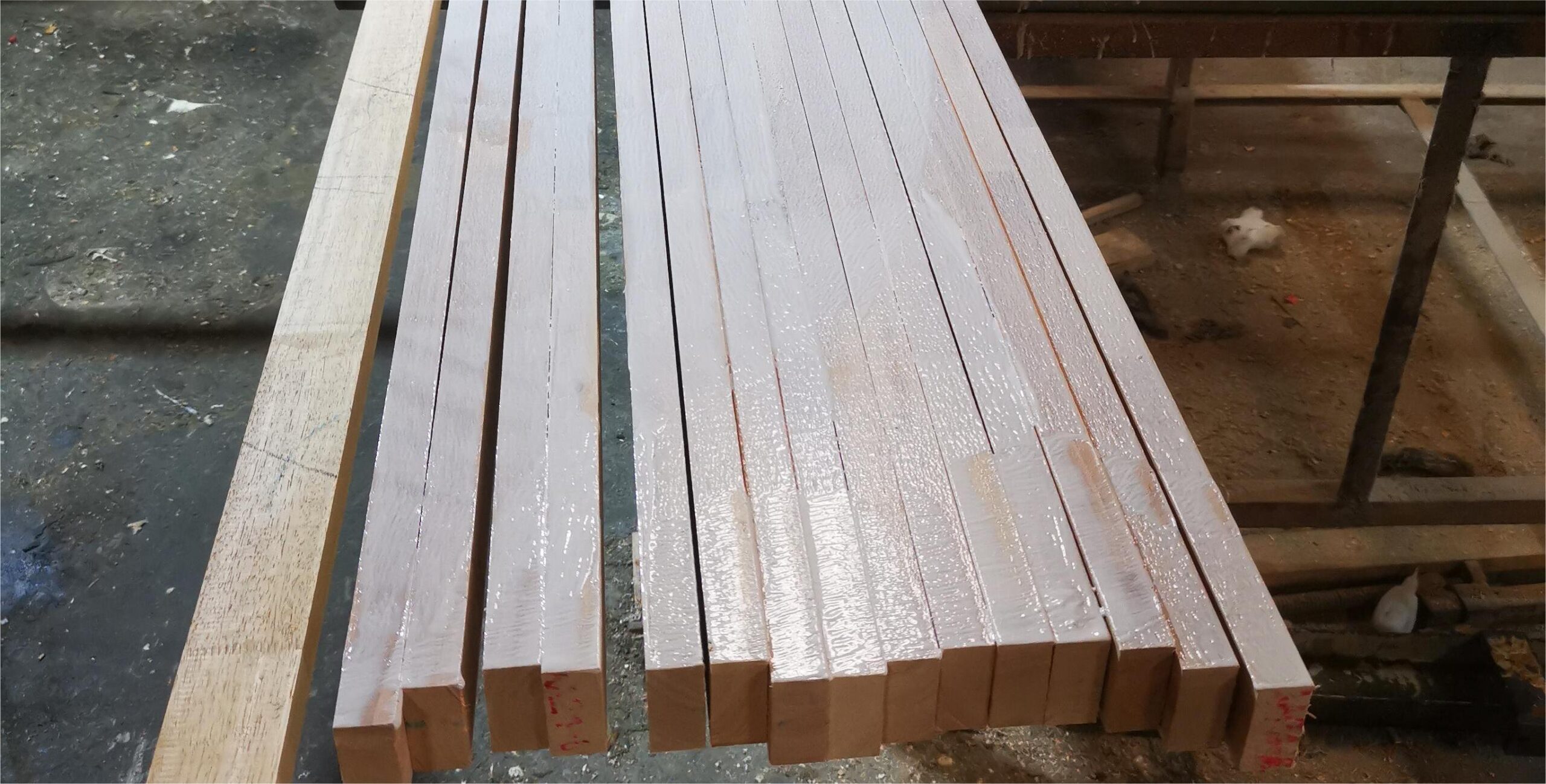
6. Oily substances (paint, detergent, etc.) enter the laminate glue
7. The interval between applying glue to the board and pressing the board is too long
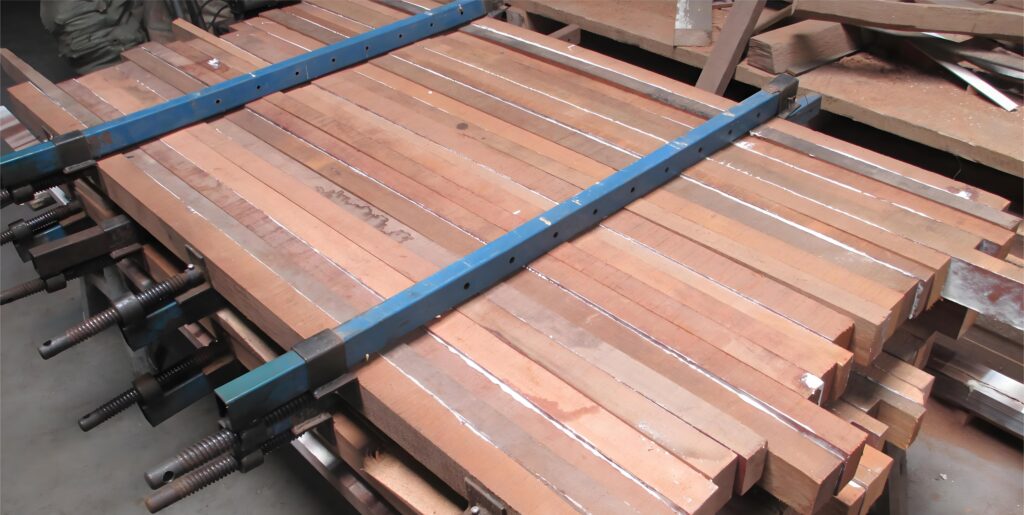
8. The surface of the board is contaminated by dust or other oily substances
9. The board is made of wood that exudes grease and has not been degreased
10. The working environment temperature of the panel is too high (greater than 40°C)
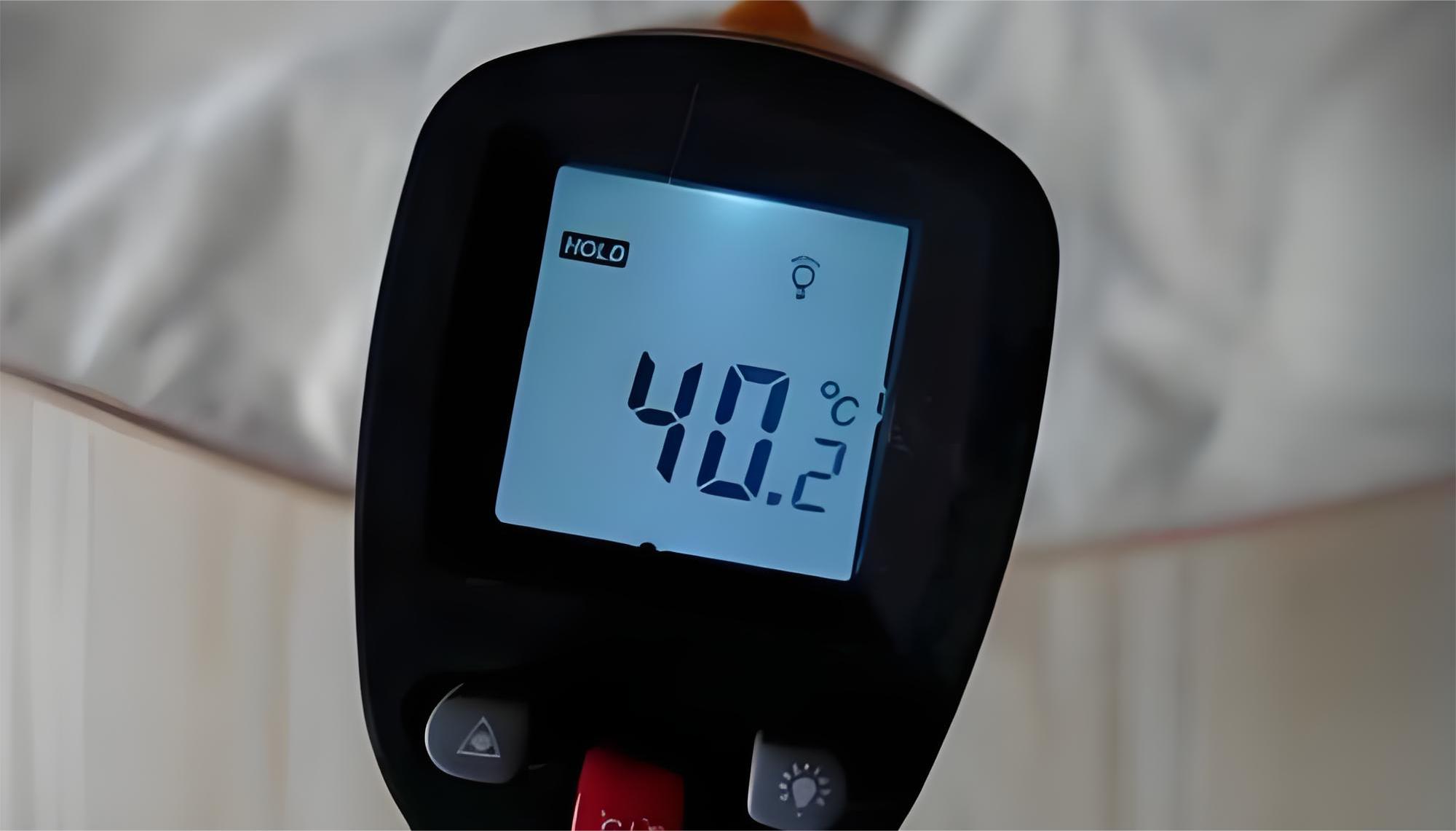
11. The working environment of the laminate is dry and the air circulation is too fast
12. The working environment temperature of the laminate is too low (less than 10°C)
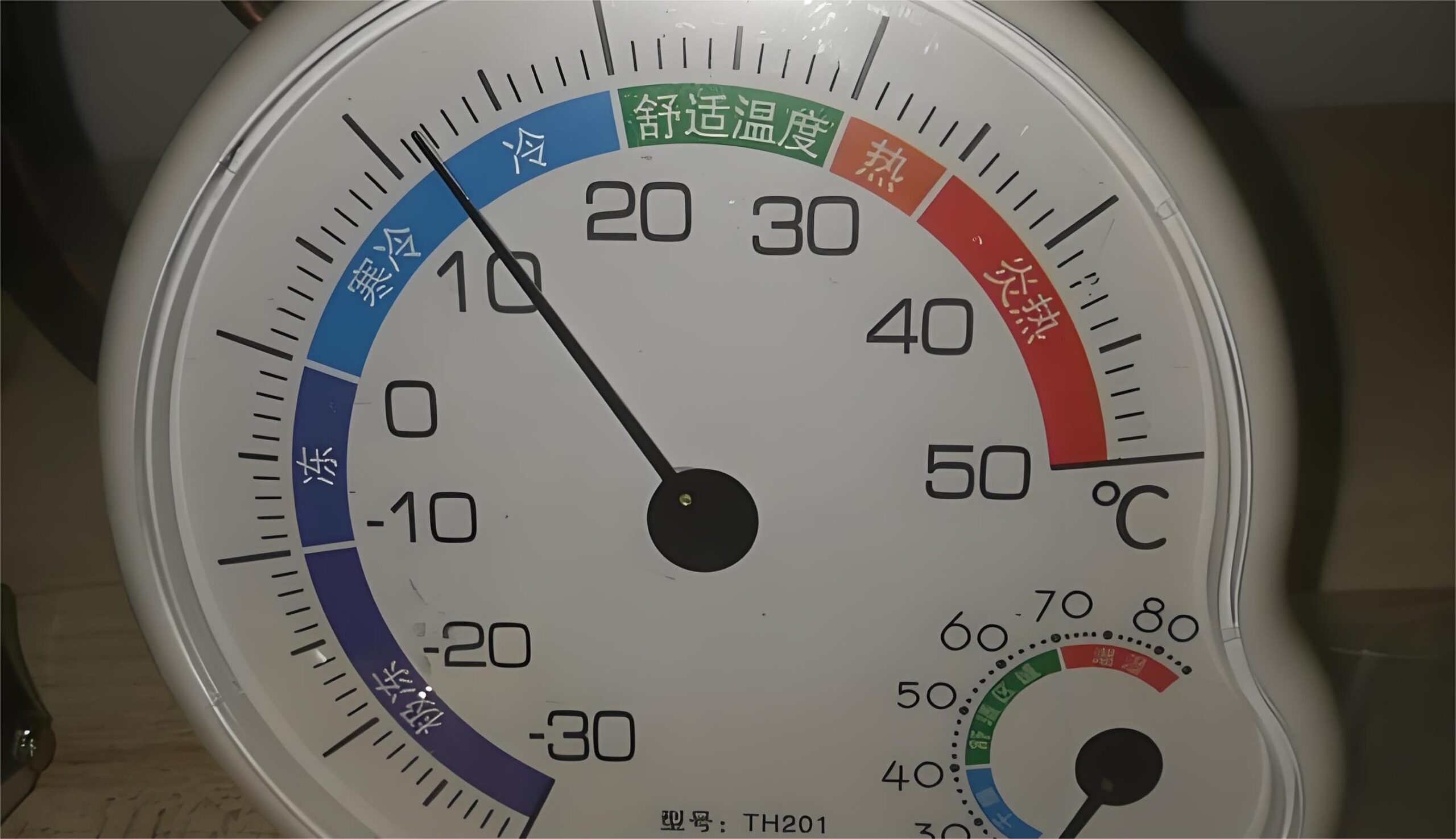
13. There is too much dust in the working environment of laminating panels
14. When applying pressure to the plate, one side has high pressure and the other side has low pressure
15. The laminate is stored for too short a time
16. The fixture is too far away from the ends of the plate (prone to cracking the ends)
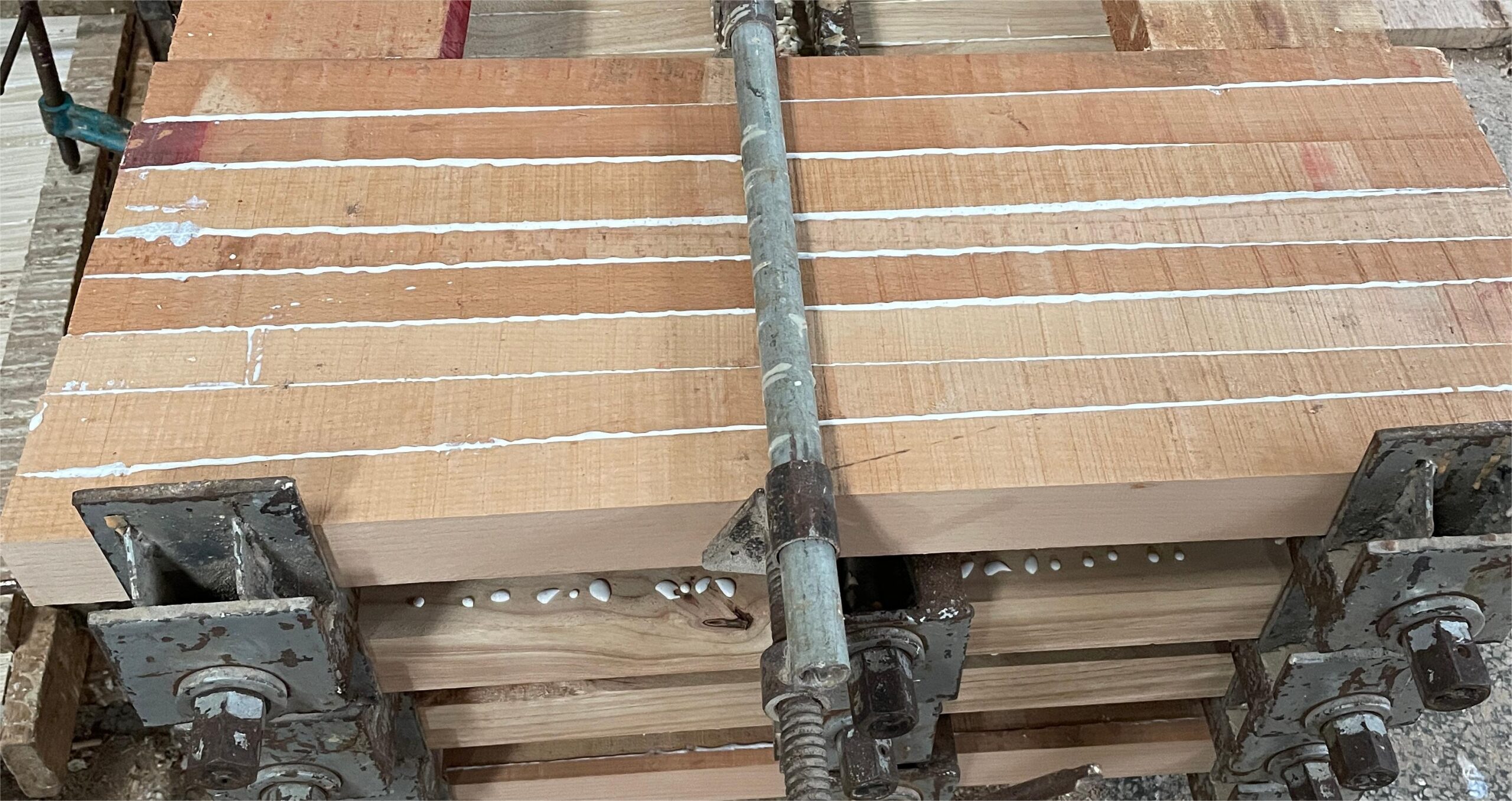
17. There are too few fixtures, resulting in adjacent fixtures being too far apart
The above reasons are the reasons why the boards crack when customers use board glue to splice them. You can check the problems one by one according to the above reasons. If you have other questions, you can consult us.