Many furniture factories now use vacuum membrane wrapping glue to bond PVC film to MDF or particle board for doors, cabinets, and wardrobes. This is mainly because such boards are fashionable and popular among consumers. Recently, when we were serving customers, we found that some furniture manufacturers had PVC film bubbles in grooves and shapes due to improper use of glue, which made the furniture manufacturers very distressed. As a glue manufacturer with many years of experience in the research and development of vacuum membrane wrapping glue, we would like to share with you the reasons and solutions for bubbles in grooves and shapes of vacuum membrane wrapping glue:
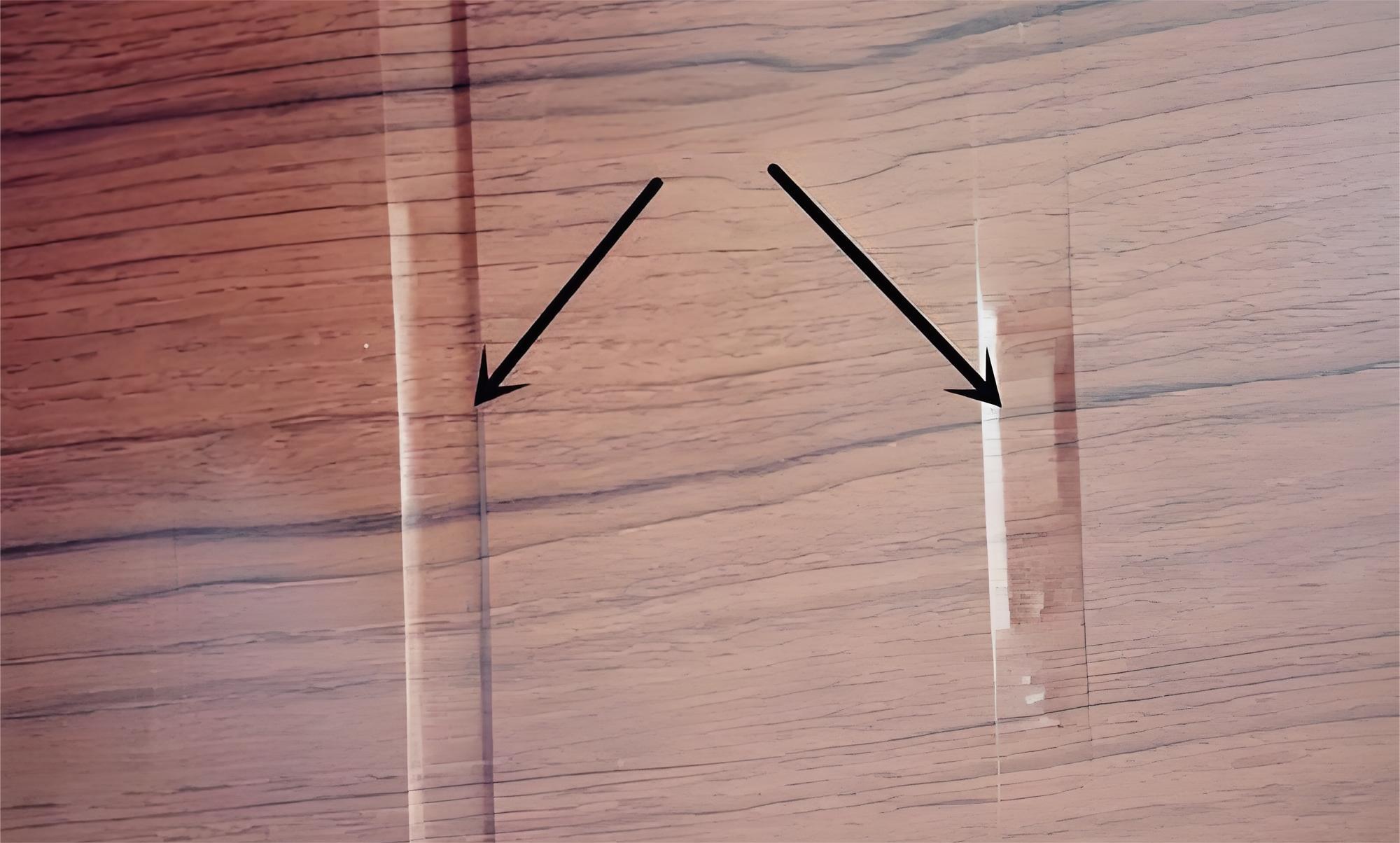
Reason 1: Wrong temperature and pressure settings of the blister machine
If the temperature or pressure of the blister machine is not set according to the standard during the blistering of the PVC film, false adhesion may occur. When the temperature of the finished product drops, the tensile force of the PVC film will increase, resulting in blistering at the shape. Given this situation, the manufacturer needs to set the pressure value of the machine to 0.4 – 0.8MPa and the temperature to 100-160℃ (depending on the ambient temperature, leather thickness, wood complexity, etc.) before using the machine for blistering, and preheat the machine before blistering and evacuate the equipment.
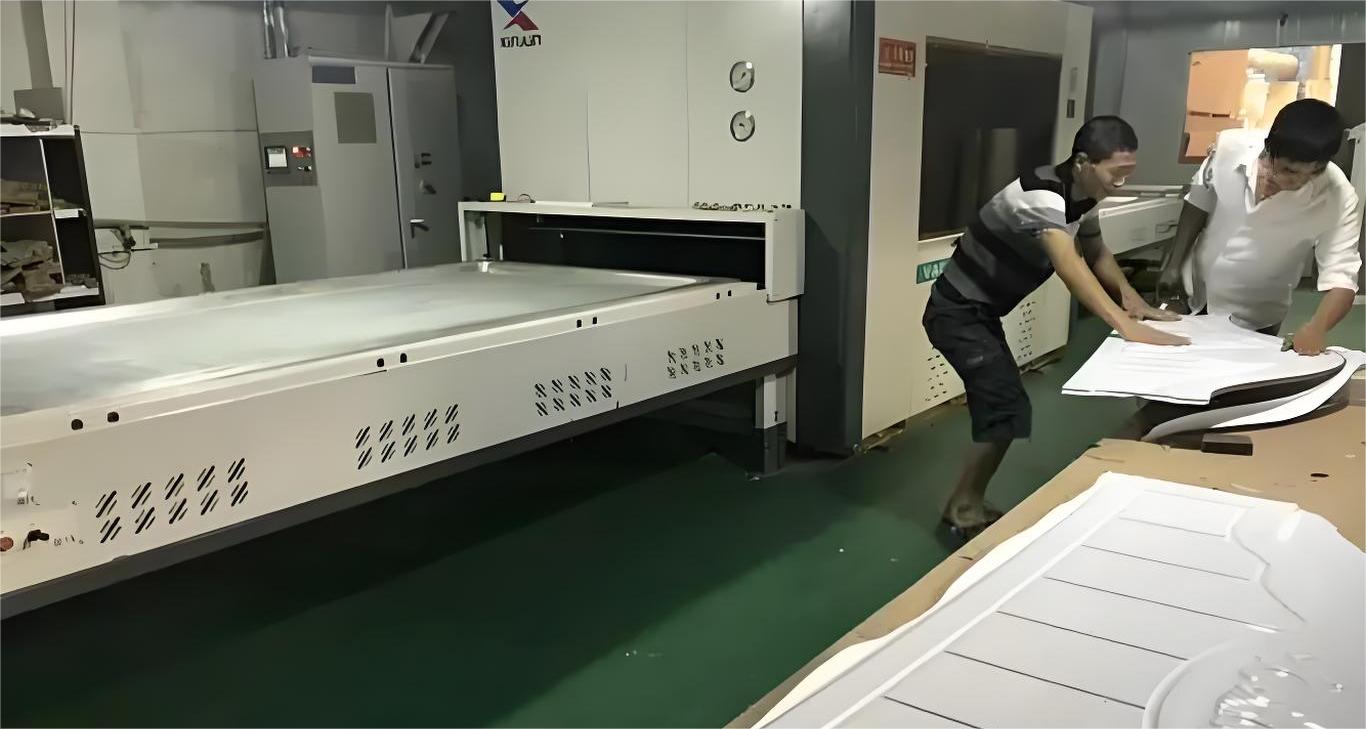
Reason 2: Insufficient glue application
There are two situations when the amount of glue applied is insufficient. The first situation is that the manufacturer applies less glue than the required value (more glue is needed at the shape) to save costs or the worker is a new employee. This will result in too little glue on the board and low bonding strength, which will cause blistering in the grooves or shapes. In this case, the manufacturer needs to apply glue to the standard value (65-75g/m² for flat surfaces, about 80-100g/m² for shapes and grooves), provide good training for new employees, and apply glue strictly according to the standard value.
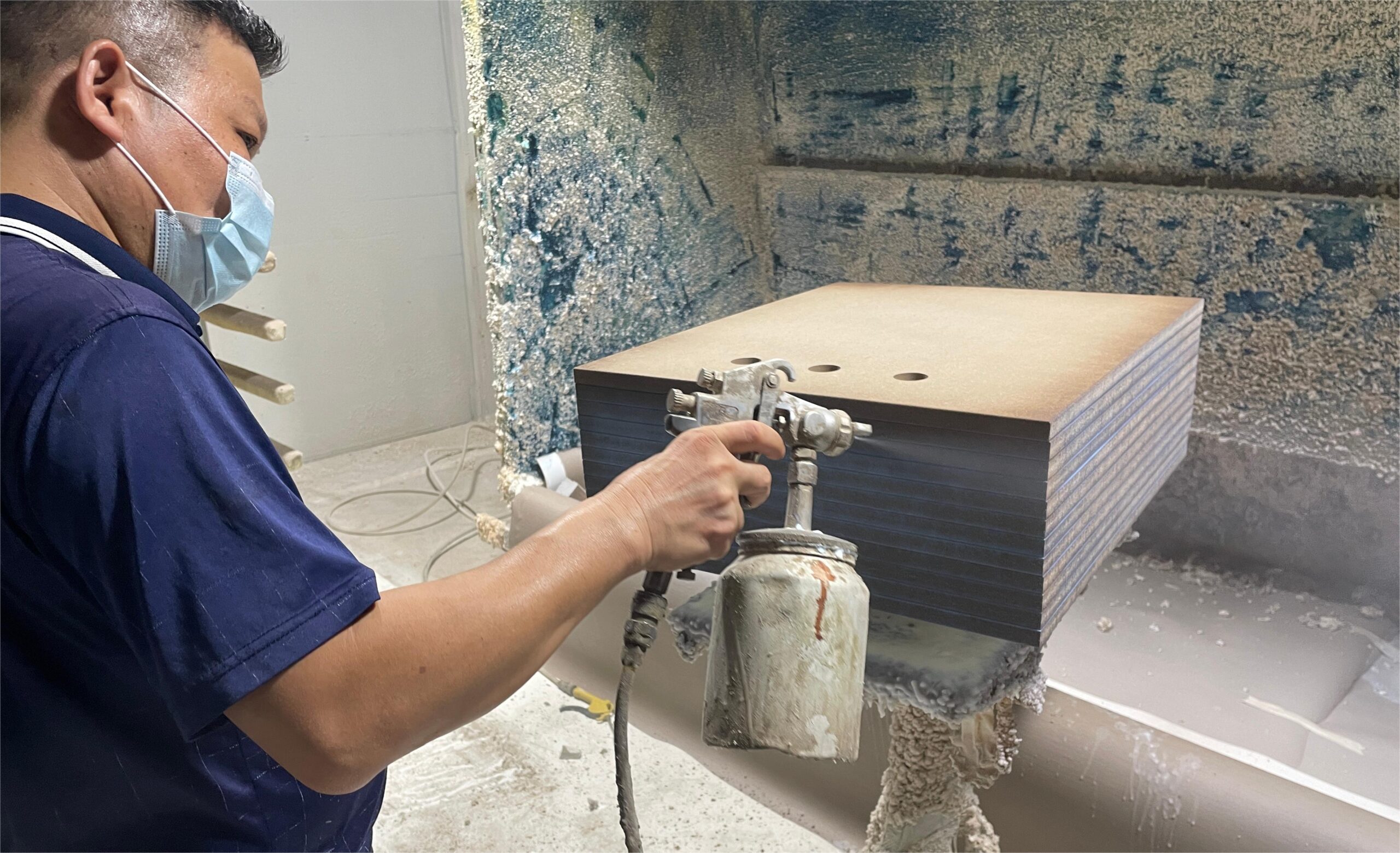
The second situation is that the board density (particle board, medium fiberboard) for blister packaging is too low. The glue is completely absorbed by the board, resulting in no glue on the board’s surface, which will also cause the overall bonding strength to decrease. In this case, it is recommended that the manufacturer replace it with a board with a density of more than 800g/cm³.
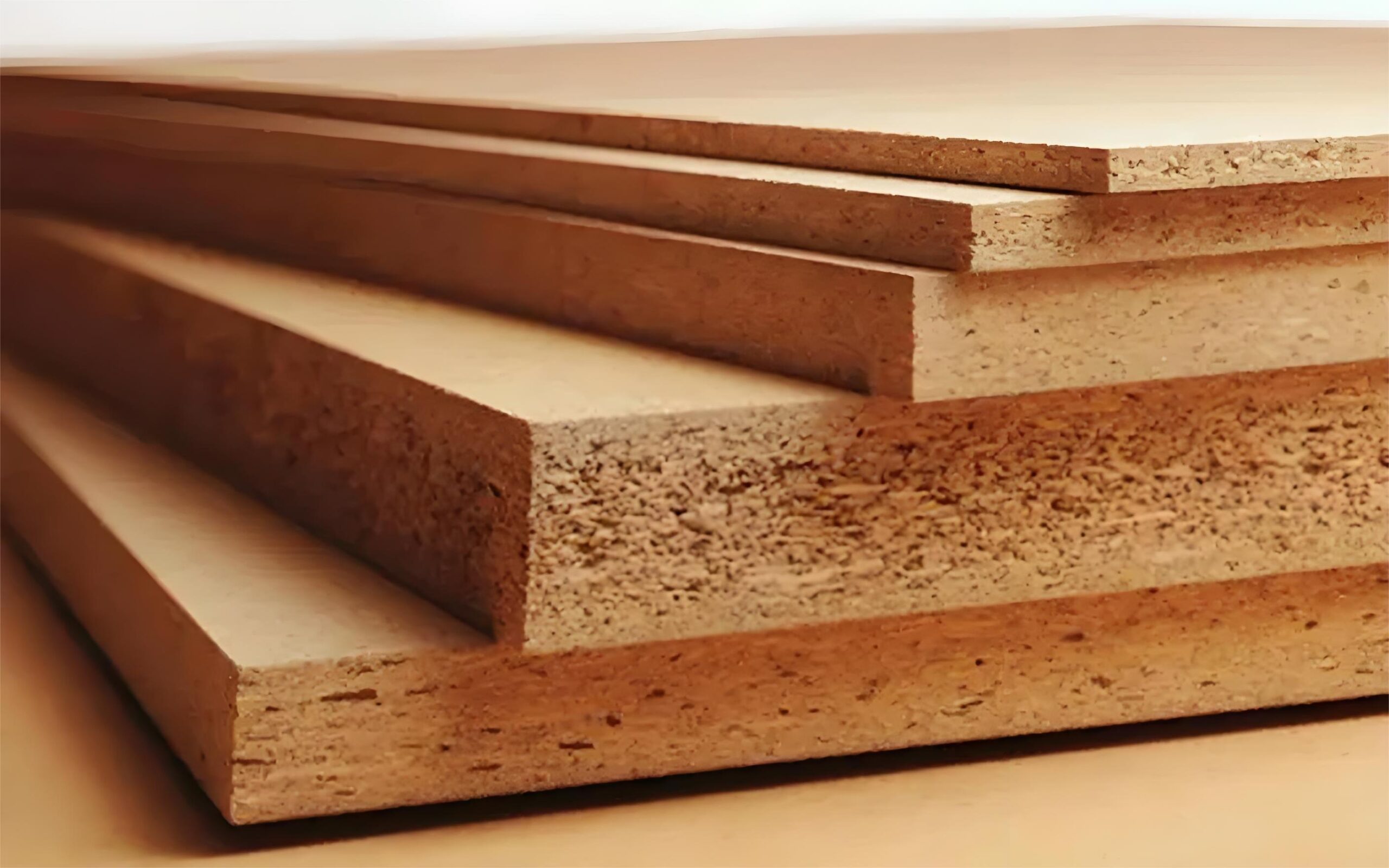
Reason 3: Insufficient preheating and blistering time
The purpose of preheating the PVC film is to soften it so that it can be well adsorbed on the board (especially the grooves and shapes) under negative pressure. However, some furniture manufacturers reduce the preheating and blistering time to improve efficiency, which will also lead to insufficient bonding strength between the PVC film and the board. Therefore, manufacturers must strictly follow the requirements of the glue supplier and the equipment factory to ensure that the preheating time reaches 100-160 seconds (depending on the ambient temperature, PVC thickness, and the complexity of the board), and the blistering vacuum time reaches 15-60 seconds (depending on the ambient temperature, PVC thickness, and the complexity of the board).
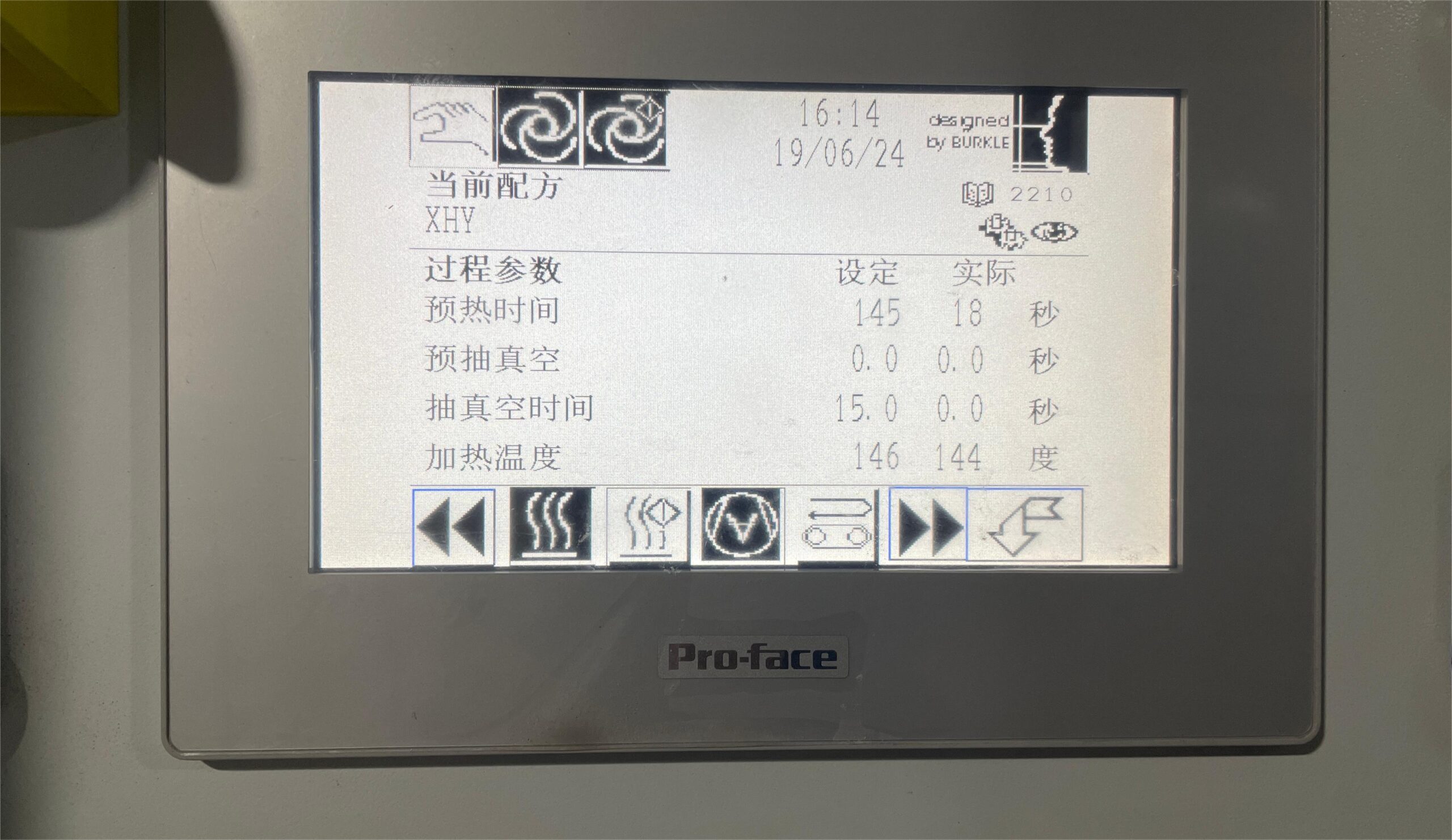
Reason 4: When blistering, remove the pressure in advance
When the product is being blistered in the blister machine, if the machine pressure is removed before the temperature drops to room temperature, it is easy to cause the PVC film to be adsorbed on the sheet and then detach again. To solve this problem, when using the machine to blister the PVC film, just wait until the temperature inside the machine cools down to room temperature (or slightly higher than room temperature), and then remove the internal pressure to prevent the PVC film from detaching from the sheet, thereby avoiding the occurrence of bubbles at the molding.
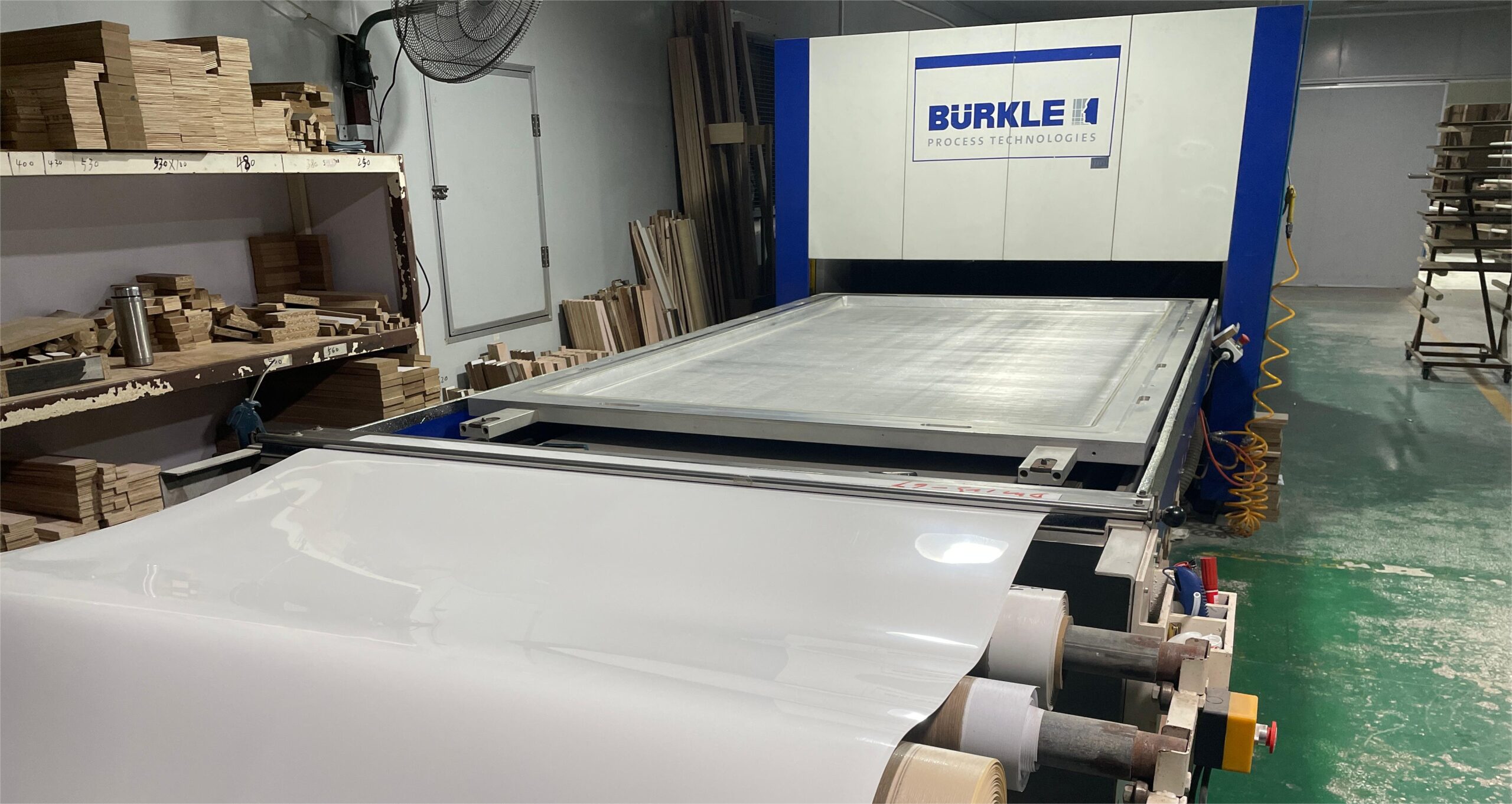
Reason 5: The glue itself has poor high temperature resistance
If the selected glue itself has poor high-temperature resistance, it is easy to cause the finished product to have grooves and bubbles in the shape during high-temperature testing. In this case, you can communicate with the glue supplier to replace the appropriate vacuum plastic suction glue and add a 5% curing agent to improve the high-temperature resistance of the glue (up to 70-75°C) and bonding performance.
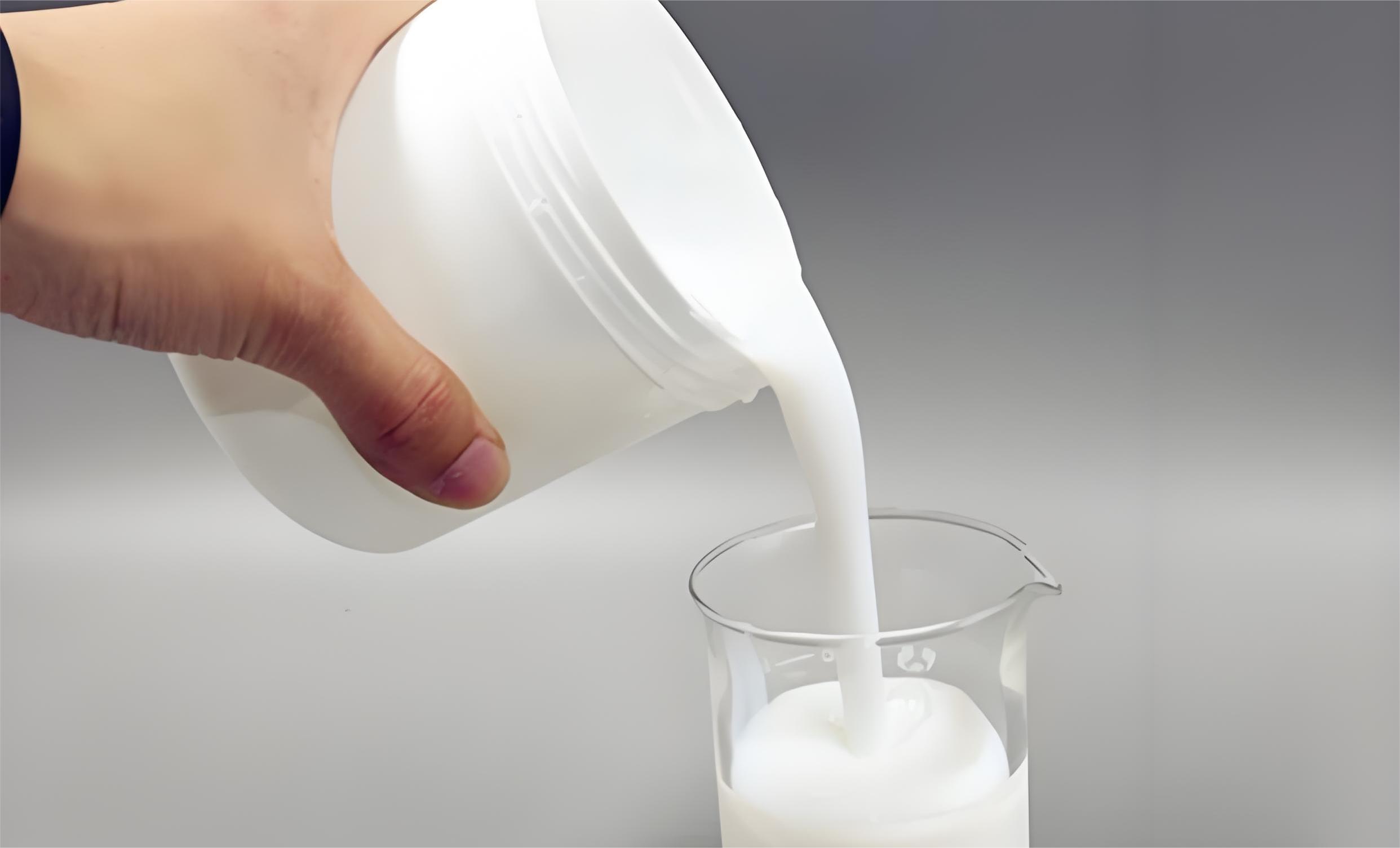
The above five reasons are the main reasons why manufacturers use vacuum membrane wrapping glue for blistering, and bubbles appear in the grooves and shapes of the plates. You can troubleshoot and solve the problems according to your own factory situation. If furniture manufacturers have any questions about the use of acuum membrane wrapping glue, you can consult us.
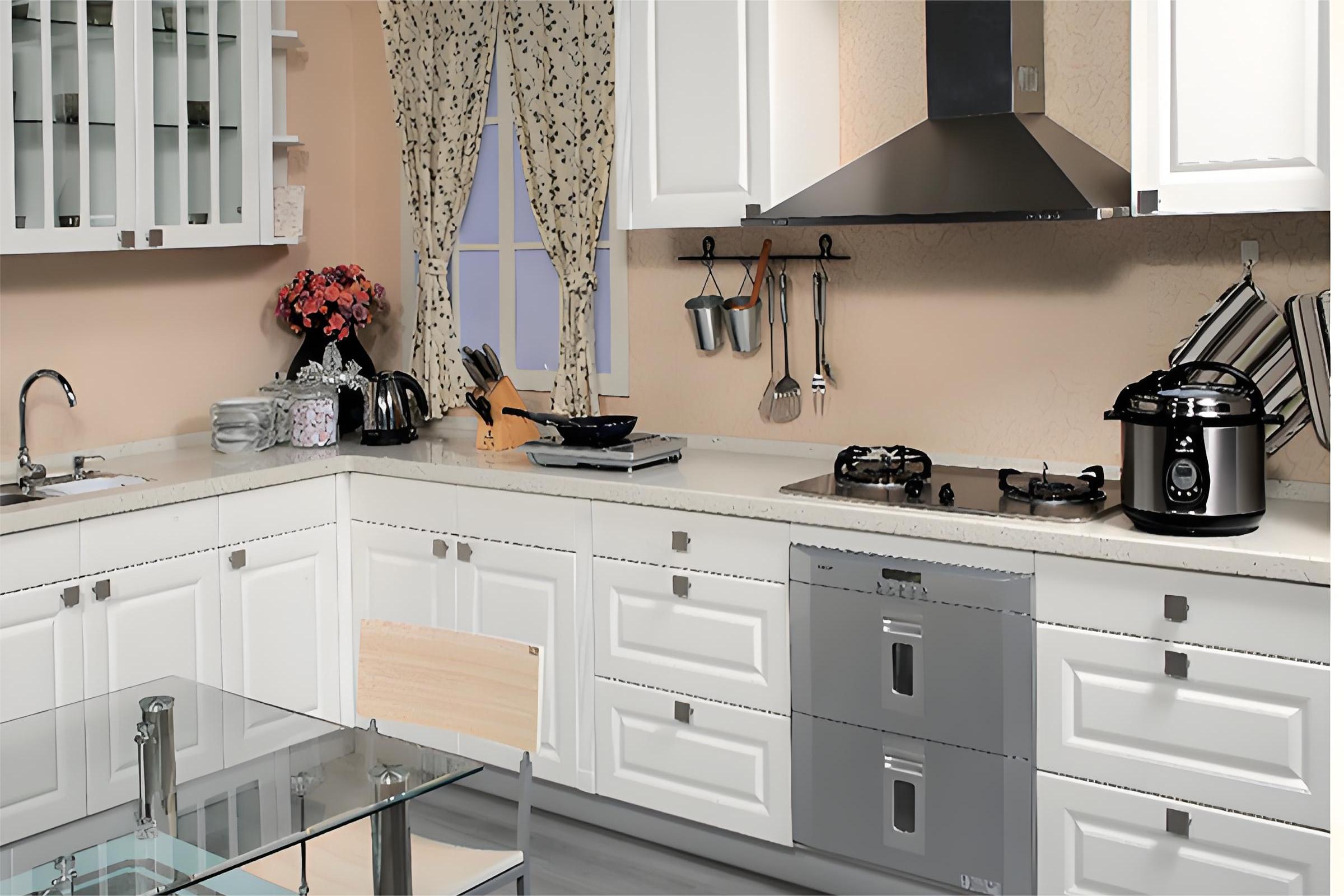