As a glue R&D and manufacturing manufacturer, when serving customers daily, we often introduce the performance and parameters of our glue to our factory customers. However, during actual communication with customers, we found that not every customer knows the properties of our glue. What do the parameter indicators mean? Let me share with you what are the important glue parameters:
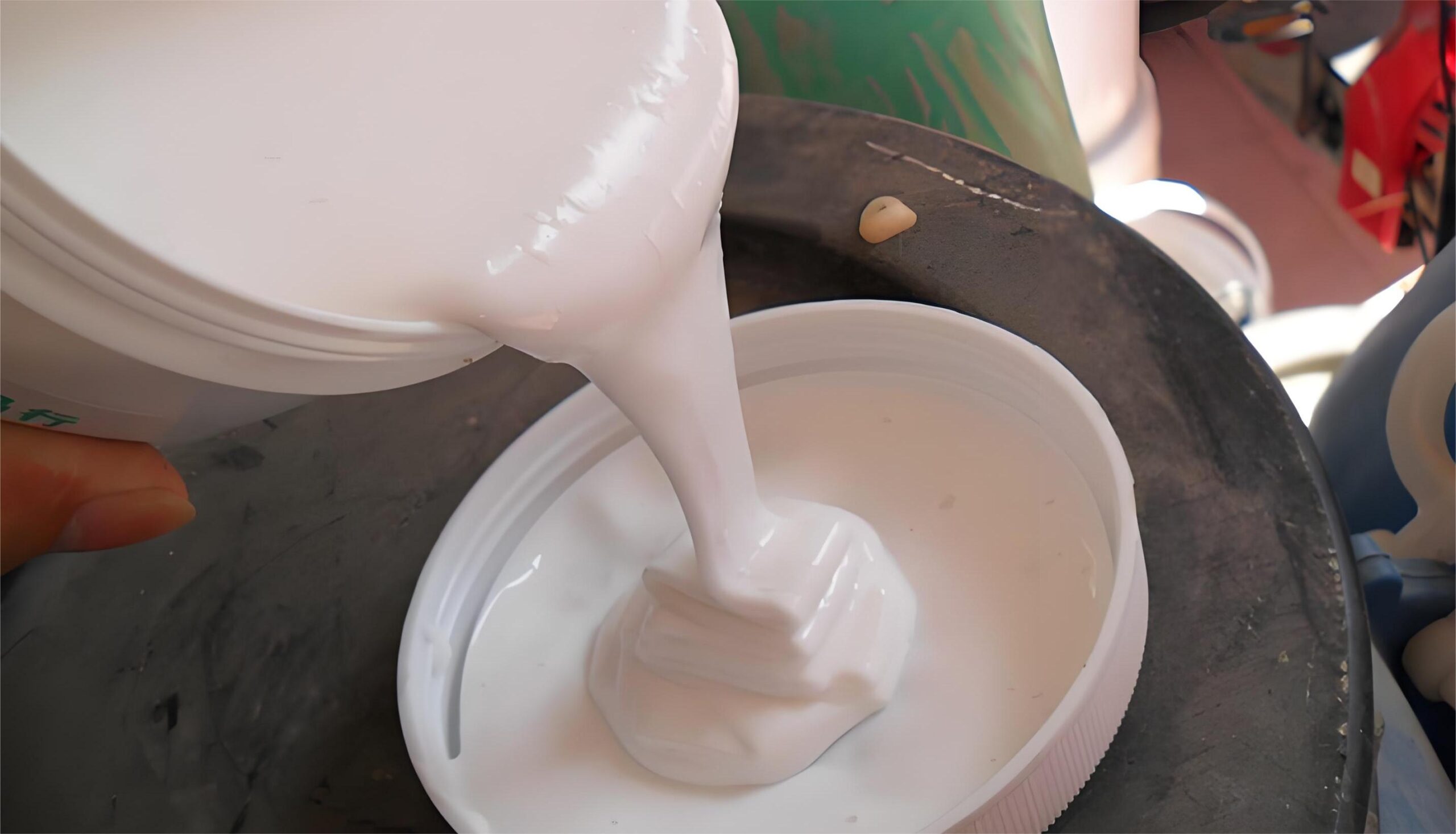
1.Viscosity
Viscosity refers to the thickness of the glue. It is measured using a rotational viscometer at a certain temperature, rotation speed, and rotor conditions. In the laboratory, a viscometer is often used for measurement; in actual production applications, it refers to the value of the glue when it is coated. The value that can be evenly distributed on the glue equipment and substrate without flowing is the appropriate viscosity.
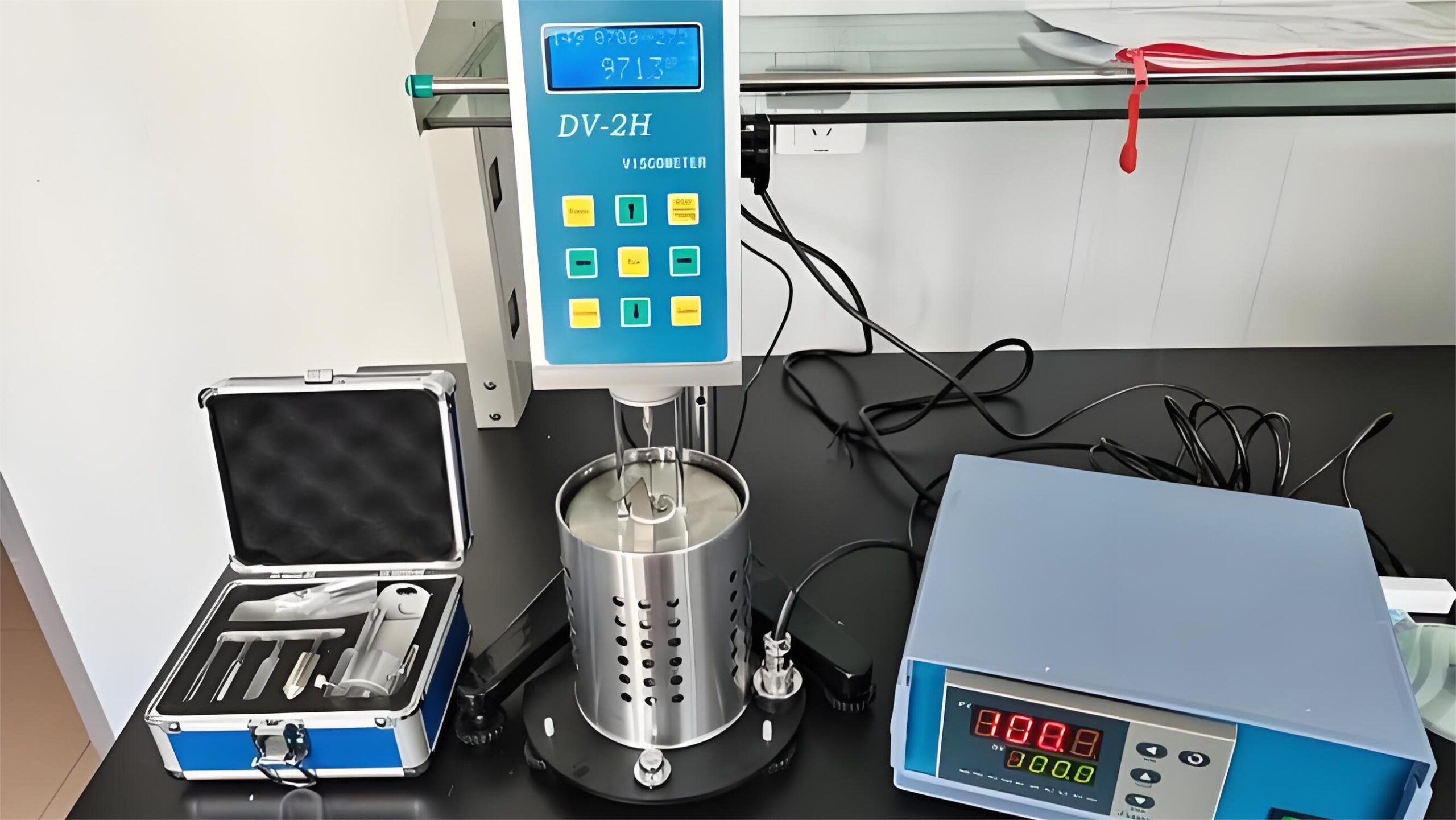
2. Solid content
The solid content refers to the ratio of the remaining solid content of a certain weight of glue liquid after the volatile substances have been volatilized at high temperatures. Laboratories often use Moisture tester. Generally speaking, the solid content is directly proportional to the time required for the adhesive to cure. Higher solid content means faster curing and faster initial strength.

3. pH value
The pH value refers to the negative value of the common logarithm of the hydrogen ion concentration in the aqueous solution and also refers to the pH value of the glue (a pH value greater than 7 is alkaline, less than 7 is acidic and equal to 7 is neutral). Generally, PH test paper is used for measurement. The PH value in glue is mainly determined by the raw materials and has no absolute relationship with performance and use. However, when the value is less than 3, the appearance of the product may be roughened in some cases and skin contact may be harmful.
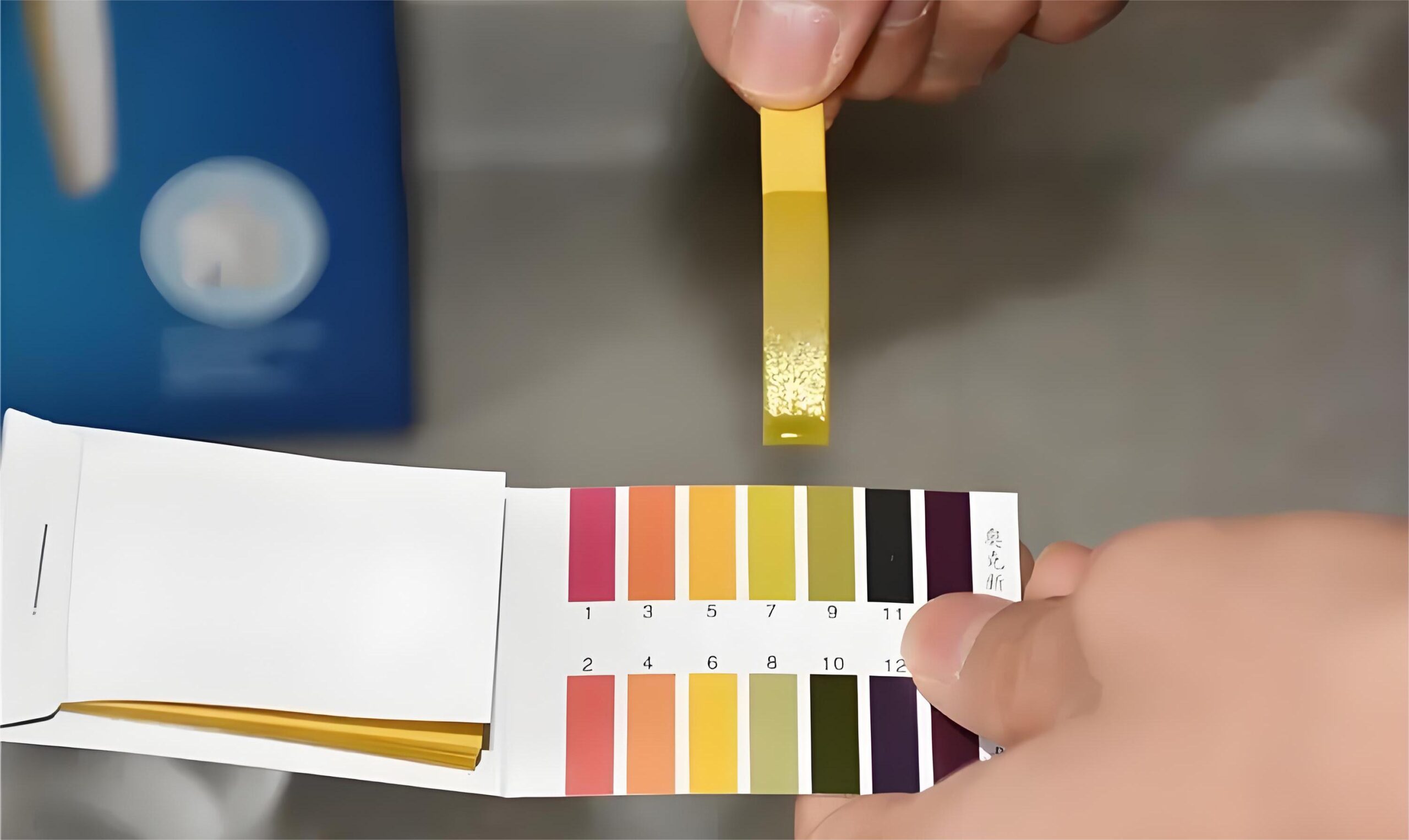
4. Density
Density refers to the ratio of mass in a specific volume. In glue, it refers to the ratio of weight to pure water. It can be measured with density meter. The density of glue will affect the amount of glue applied. Glue with a small density value will generally have a smaller amount of glue applied.

5. Moisture content of substrate
The water content of the substrate refers to the ratio of the total internal and external molecular water contained in the substrate to be bonded to the weight of the substrate itself. It is generally measured using a wood water tester. The optimal water content of the substrate is 8-12%. When the water content is too high, the cohesive strength of the board will be low and the tensile strength after lamination will be low. When the water content is too low, the surface energy of the board will be low and the strength after lamination will be low.
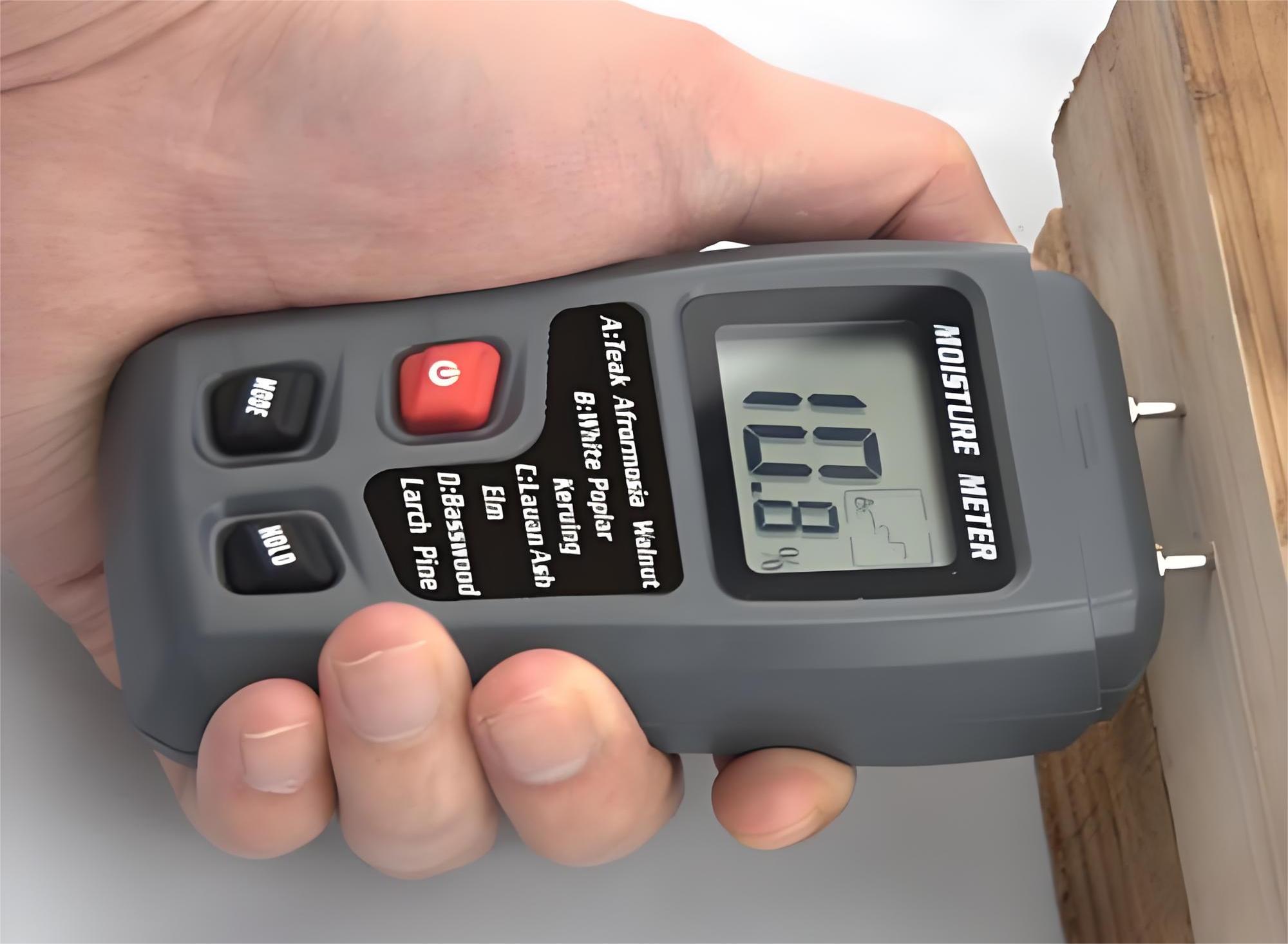
6. Glue amount
The amount of glue applied refers to the ratio of the total weight of glue applied to the substrate to the area. It can be measured using a mass balance scale and calipers. Generally speaking, between the minimum glue amount and the maximum glue amount required to meet the bonding requirements, a low glue amount will result in low bonding strength and low substrate breakage rate, while a high glue amount will result in high bonding strength and high substrate breakage rate.
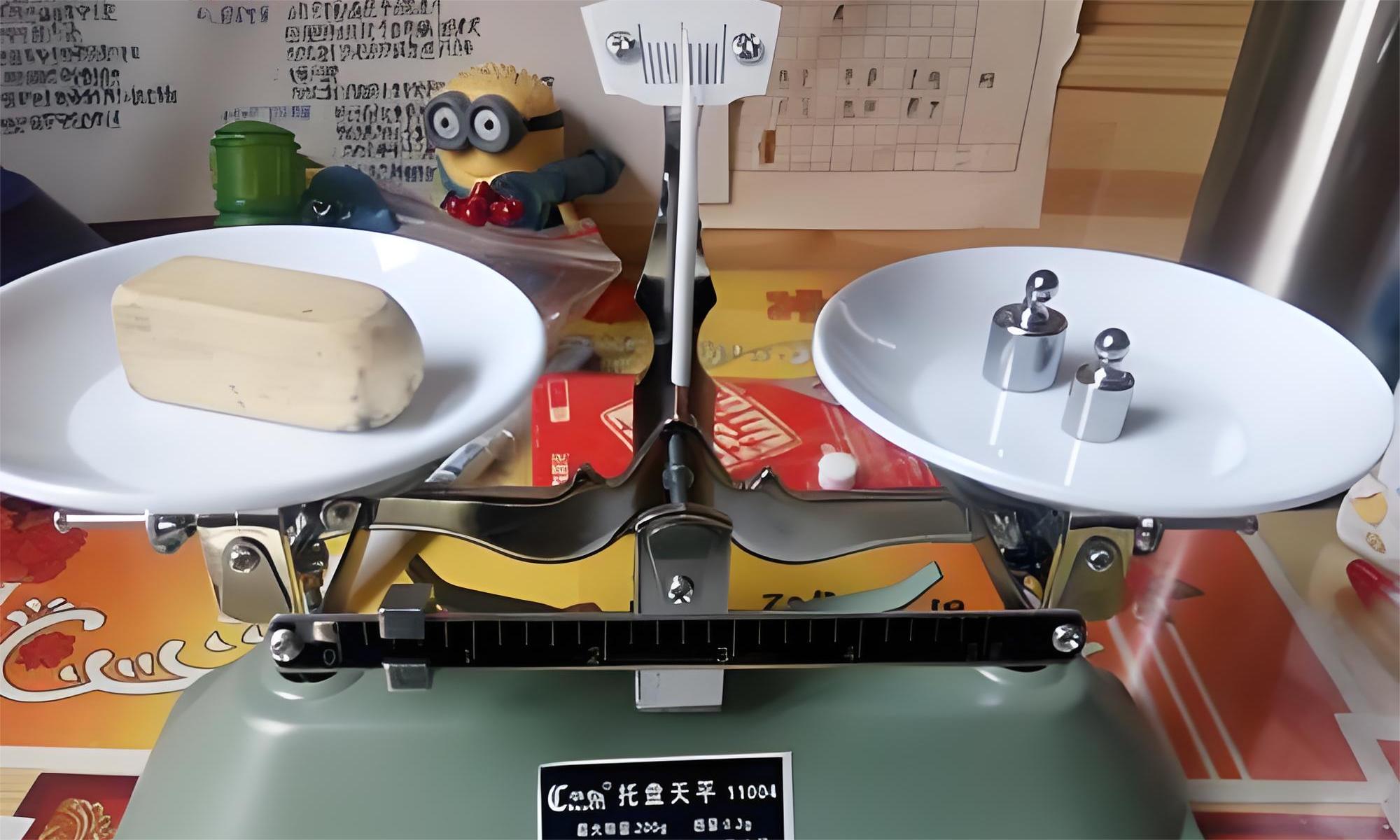
7. Operating ambient temperature
The ambient temperature of use is the ambient temperature of the bonding material at the site where the glue is used for more than 24 hours. It can be measured with a thermometer. Only when the bonding material is above the required temperature can the glue form a good bond. Only the temperature of the substrate or the glue can be used. If the temperature is reached, otherwise it will be lower than the temperature requirement, which will cause rapid heat loss during use and affect the bonding effect.
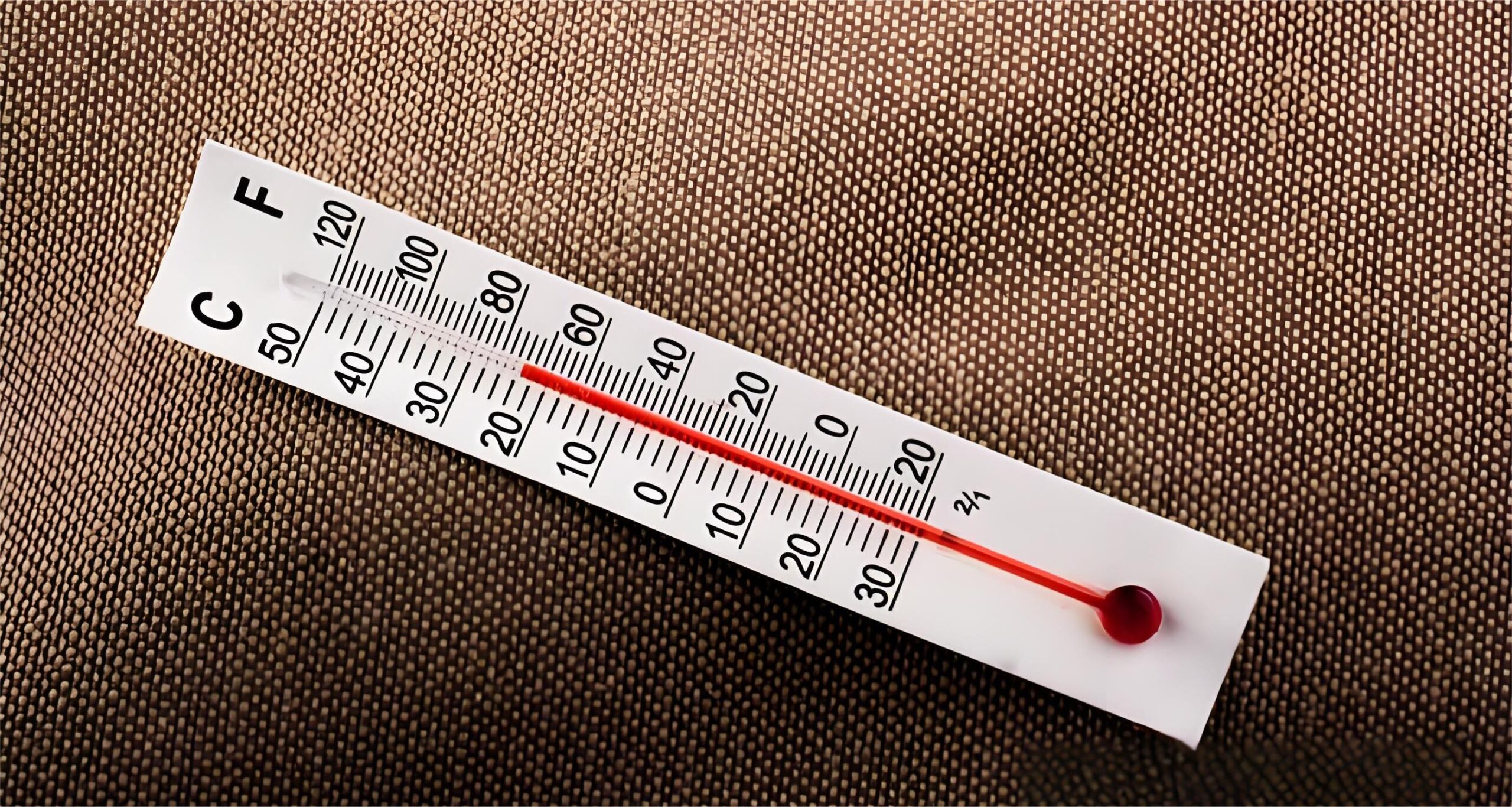
8. Curing time
Curing time refers to the time required for the glue to naturally dry and solidify to reach the maximum bonding strength (it will be affected by changes in environmental conditions, such as the curing time becomes longer when the humidity is high, and the curing time becomes shorter when the temperature is high). You can use a timer to measure it.
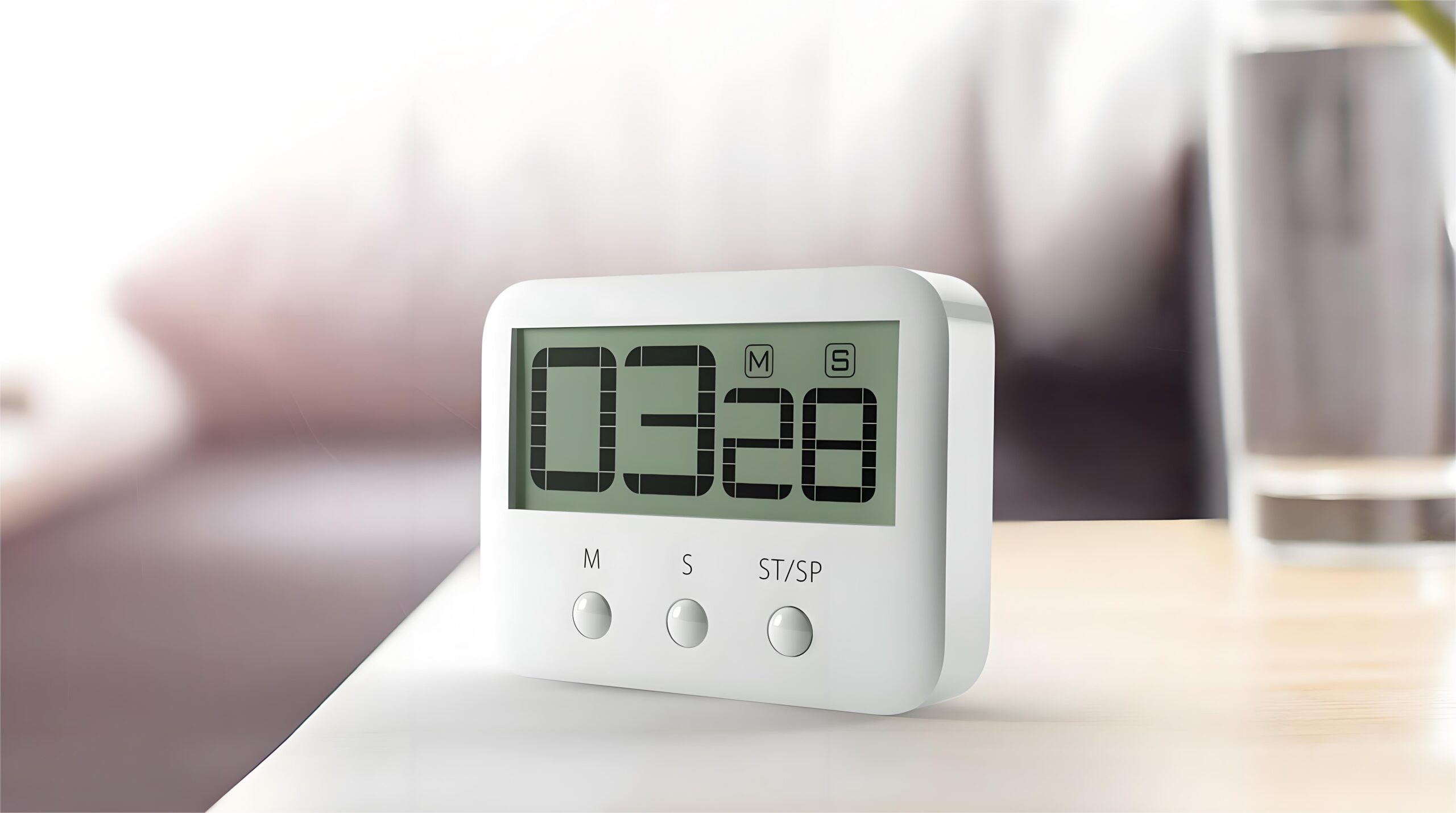
9. Pressing temperature
The hot pressing temperature refers to the highest temperature that can be accepted by the bonding substrate for extremely short periods of heating, which can be measured with a Infrared thermometer; Heating the substrate can quickly penetrate the adhesive and increase the surface strength of the bonding site to make it easier to bond.
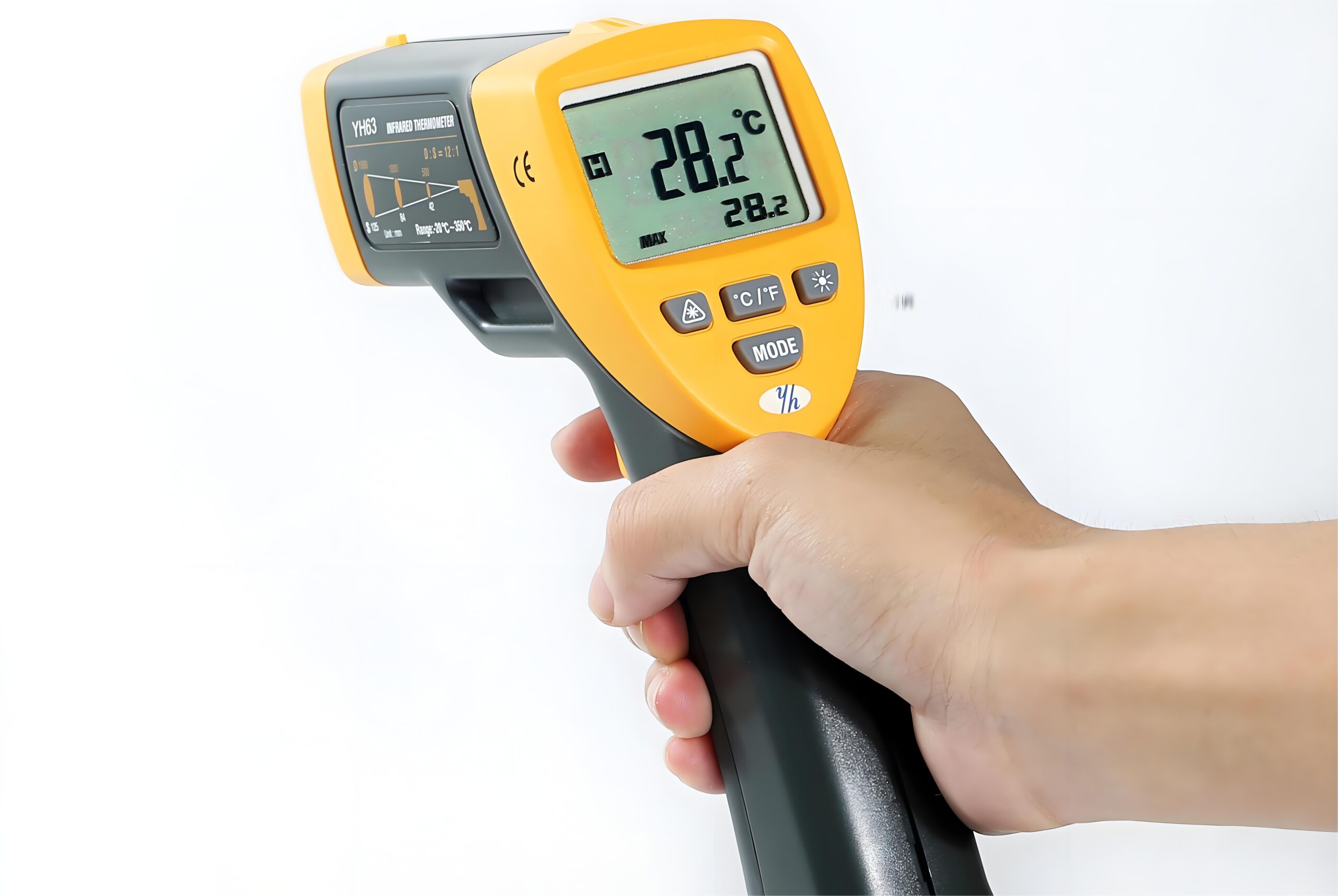
10. Storage time after pressure relief
The storage time after pressure relief refers to the natural drying time of the substrate that needs to be bonded under pressure after the pressure is removed, which can be tested using a clock. The adhesive substrate that needs to be pressurized will form internal cohesion after the adhesive solidifies. To prevent the rebound of the adhesive substrate, it needs to be aged for some time to reduce its cohesion.
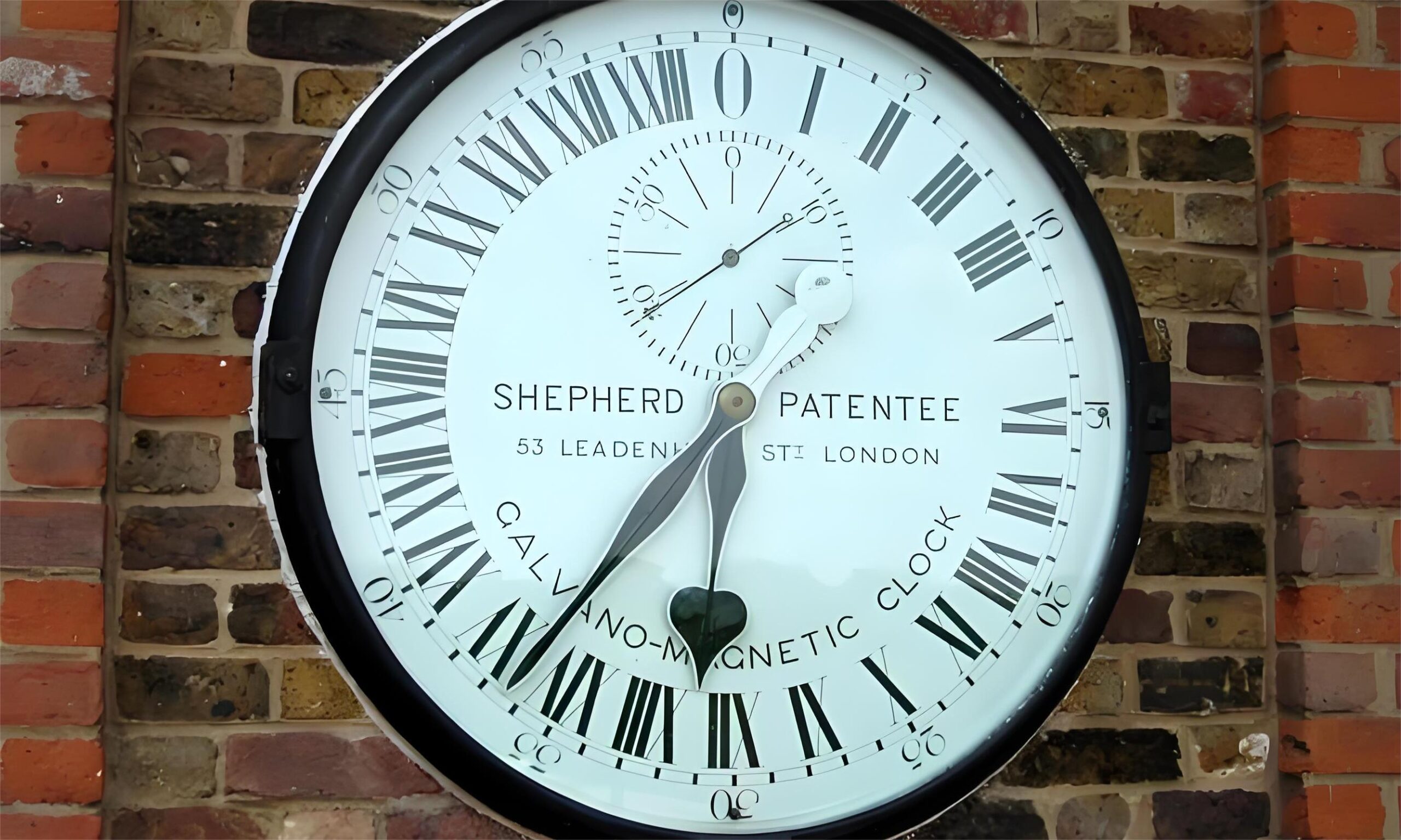
11. Peel strength
Peel strength refers to the unit tensile force in the 180-degree direction after a flexible material is bonded to a rigid material. It is commonly measured with a tensile gauge. The higher the strength, the better the adhesion and penetration performance of the adhesive, which is related to many factors such as the surface tension of the substrate, the cohesive strength and permeability of the board surface, the humidity of the board, the use temperature, the cohesive strength of the adhesive, and the use process.

12. Temperature resistance
Temperature resistance refers to the maximum and minimum temperatures that the glue and substrate can withstand after bonding. It can be tested with a thermometer. The heat resistance and cold resistance after bonding are related to many factors such as the surface tension, toughness and hardness of the substrate, fitting shape, sheet permeability, adhesive adhesion, and film hardness.
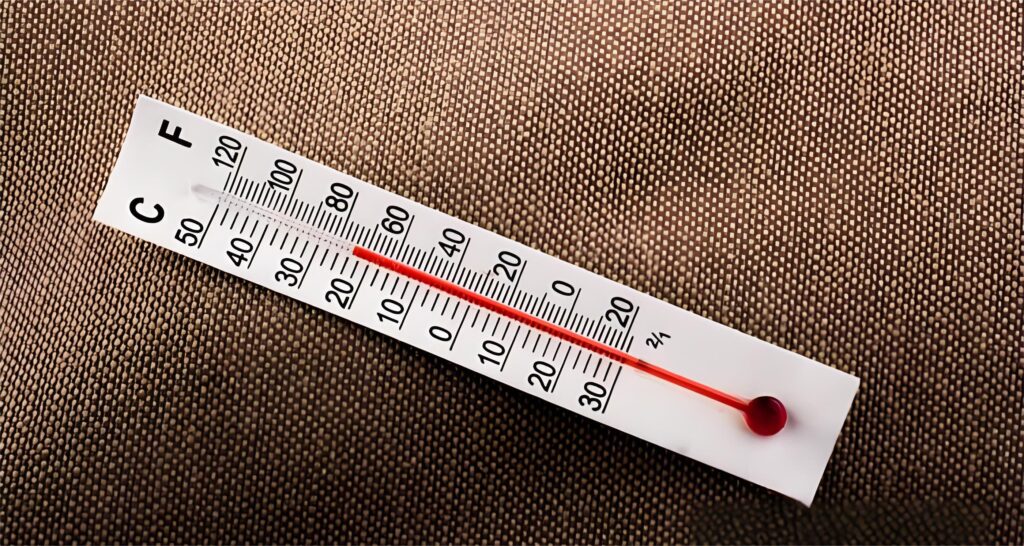
The above are 12 important parameters for factories when using adhesives. If you need consultation on other parameters, please contact us.